Twenty million students are currently enrolled in colleges and universities in the United States. While enrollment continues to be flat, the availability of campus housing still lags behind. Housing shortages afflict campuses nationwide. Undergraduate and graduate students, as well as faculty and staff, often base their decision to attend colleges and universities on housing availability and options.
Both public and private institutions are also increasing the use of public-private partnerships (P3), collaborative design-build, and integrated project delivery (IPD). Design-build and IPD work well because they give the team the opportunity for the kind of collaboration needed on higher-education projects. No matter what the delivery system, long-term owners like universities embrace the use of precast concrete for their new construction projects. Here is an example of how precast concrete systems earned high marks in a college setting.
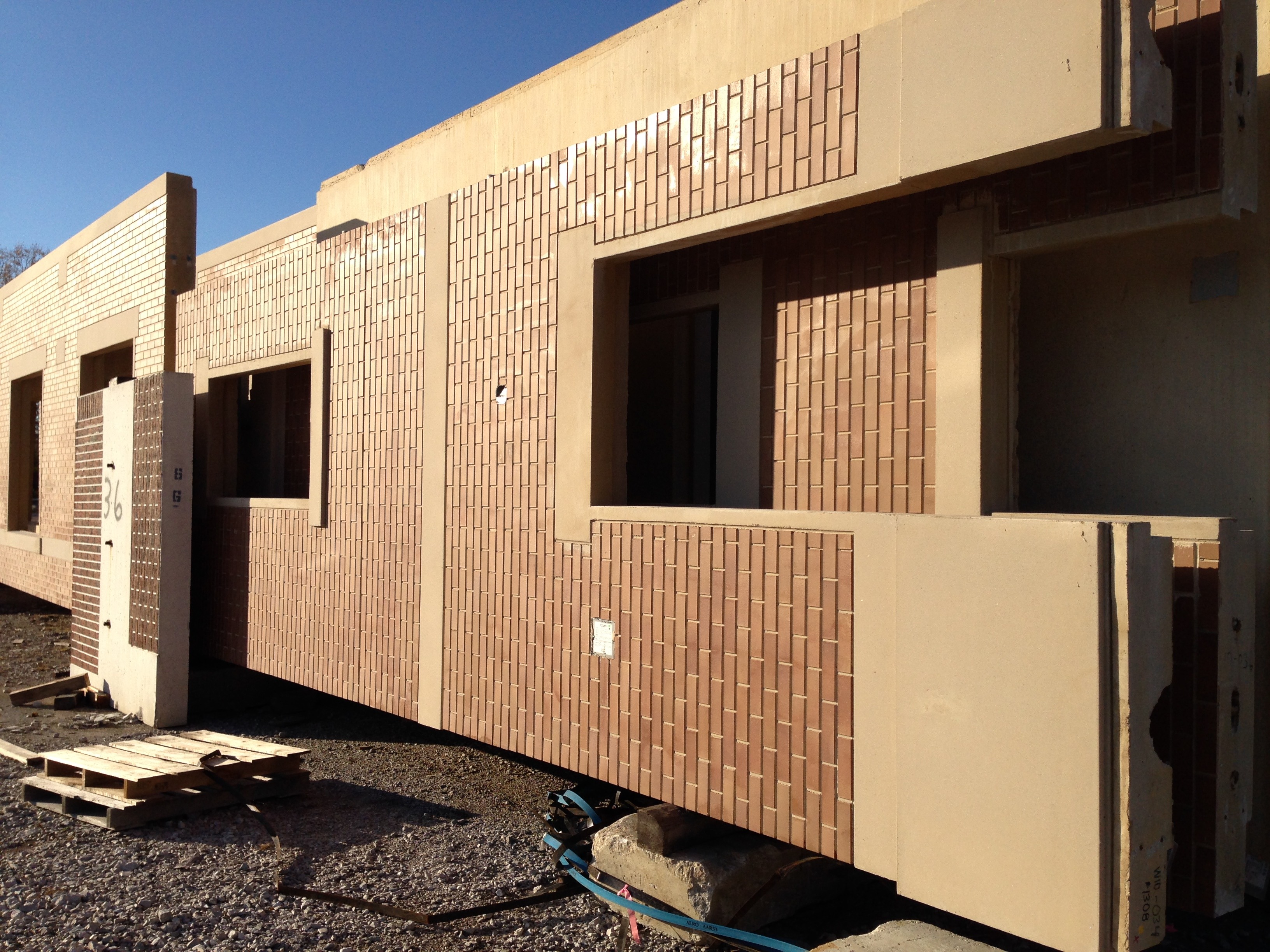
Beacon Hall, Valparaiso University, Valparaiso, Ind.
Valparaiso University (Valpo) was founded in 1859 as one of the first coeducational colleges in the United States. A private institution operated by the Lutheran University Association, Valpo enrolls about 4500 students and covers 350 acres. Almost two-thirds of students live on campus, as university regulations require nearly all underclassmen to live in residence halls.
An integral part of the Valpo master plan is visual coherence and maintaining a consistent design standard. This vision is to be reflected across the campus, regardless of when and where the structures were built. As part of the transformation, the design-build team of Mortenson Construction in Itasca, Ill., and FGM Architects in Chicago, Ill., were engaged to provide a new student residence hall on the northern edge of campus.
The 85,000-ft2 Beacon Hall was the first suite-style residence hall at Valparaiso University and the first to be constructed with a precast concrete system. The building’s Collegiate Gothic architecture complements the campus housing aesthetic and includes four-, six-, and eight-bed suites. The residence hall also features a wide range of flexible common areas including study spaces, computer rooms, a nondenominational prayer room, laundry rooms, kitchenettes, ping-pong and billiards room, and an outdoor courtyard.
“Beacon Hall embodies Valparaiso University’s vision for staying true to its roots while embracing the changing needs of college students. The residence hall incorporates design elements from existing campus buildings while offering living arrangements and amenities popular with students and parents alike,” says Joel Sandridge, project development executive with Mortenson. Sandridge was project architect with FGM Architects during the Beacon Hall project.
The new building was sited to create an attractive urban streetscape close to the front sidewalk. “Beacon Hall formed the new northern gateway, so it was important that it be prominent and well-designed,” explains David Yandel, principal at FGM Architects.
He adds, “The Collegiate Gothic style includes gabled roofs, punched openings, and is solid in mass and composition. All those features can be accomplished with a precast solution.”
The university provided input on the selection of materials, but because of the schedule, it was not a lengthy design process. “We seemed to get things right very quickly,” describes Yandel. “There was strong direction from the university, and they were exceptional to work with, along with the rest of the team.”
“Valparaiso University insists on utilizing high-quality systems and materials. Using precast concrete gave them a lot of advantages: a 75-year facility life as well as an accelerated 12-month schedule,” recalls Sandridge.
The Beacon Hall project was design-build, with Mortenson leading the team that included FGM Architects, KJWW Engineering (now IMEG), and Coreslab Structures. Mortenson has extensive precast concrete experience in all higher-education segments. “Customers are starting to understand that precast is a great solution not only for speed, but quality as well. We have used precast extensively for speed to market and the institutional high quality that are so important to these long-term owners,” explains Sandridge.
“The design-build team had to examine how to deliver this project as fast as possible. From notice to proceed to completion date, we were up against a tight schedule,” he recalls. Design-build and precast concrete were both essential to meeting that deadline.
Mortenson briefly considered other systems, but the idea of having one subcontractor to supply the entire solution— structure and enclosure—was appealing. “When you work with light-gauge steel or other systems, it requires a lot of other trades and complications. For example, the precast ceiling required just a skim coat on the underside to provide a high-grade finish, so additional materials were not required,” describes Sandridge.
—————-
You can read the rest of this article in the latest issue of Integration Quarterly, DBIA’s new digital magazine, available now!