Issue 3 of 2015
One of the key findings of the 9/11 Commission Report, which sought to document the events and intelligence lapses leading up to the 9/11 terrorist attacks, was that miscommunication between agencies and a lack of collaborative integration between the FBI and the CIA led to intelligence breakdowns and the oversight of key threats. The world is a different place today, and better collaboration between various agencies has improved national security. The use of the collaborative design-build project delivery method has also become more common, rising more than ten percentage points since 2001 to almost 40 percent of the non-residential market today. That’s because design-build offers faster delivery, accompanied by higher quality and owner satisfaction. The collaborative nature inherent in the delivery method also lends itself to meeting anti-terrorism requirements now in place for military buildings.
The Department of Defense (DoD) has recognized the dangers to its facilities worldwide and, in recognition of that fact, has set minimum standards for the security at those facilities. Established within the DoD Unified Facilities Criteria (UFC), the standards “represent a significant commitment by DoD to seek effective ways to minimize the likelihood of mass casualties from terrorist attacks against DoD personnel in the buildings in which they work and live.” The criteria detail the dangers, including building collapse, flying debris, airborne contamination, a building layout that may hinder reaching safety or the lack of a means to notify building occupants of danger and how to respond. The DoD Antiterrorism UFCs establish the protective criteria based on the assessment of the assets within the facility. Based on the value of the assets and the local threat, a protection level is determined. That protection level may vary from no requirement for low occupancy, low value facilities, to high level of protection for high value assets. The UFC sets out plans not only for new construction, but also for gradually updating existing facilities to the necessary level of protection.
“Designers and builders of Air Force facilities are responsible for minimizing opportunities for terrorists to threaten or target members, contractors and their families in DoD occupied space,” said Ben Kindt, Chief of the Standards and Evaluation Branch in the Air Force Civil Engineer Center Facilities Engineering Directorate. “The UFC provides efficiency and reliability by delivering consistent standards that ensure crucial security features are incorporated into the planning, design and construction of every facility.” Three projects that won 2014 Design-Build Project/Team Awards from DBIA went above and beyond those performance requirements: the Naval Hospital at Camp Pendleton in California, the UEPH Schofield Barracks in Hawaii and the Battlespace Environment Laboratory at Kirtland Air Force Base in New Mexico. All were commended by the project owners for their work with the DoD personnel to ensure that the buildings were not only functional, but would provide the necessary level of security.Since design-build is used on more than 80 percent of military projects, successful design-builders have learned to work with the UFC, and, in fact, there is a section of the UFC – Section 1-12.4 – that is specifically for design-build contracts. In accordance with DBIA Best Practices, it allows the agency writing the RFQ/RFP to set performance requirements – specifying specific design loads, standoff distances and so on – and then rely on the prospective design-builders to engage their creativity and design what is required.
Naval Hospital at Camp Pendleton Replacement
Situated at the edge of the base, adjacent to a residential area, the existing Naval Hospital at Camp Pendleton in California did not benefit from the perimeter protections provided to facilities inside the base. In addition, since many of the patients at the hospital will be civilian adults and children, they would be more vulnerable to attack.
“The existing hospital did not meet current space planning guidelines as specified by the UFC 4-510-01, or the Unified Facilities Criteria-Design: Medical Military Facilities,” explained Angela Webster, Lieutenant Commander in the Medical Services Corps, and Health Facility Planning/Project Officer on the project. “Simply put, this new hospital facility design was fresh, current and dynamic. It was not a 10-year-old shelved design waiting to be funded, then requiring validation and updates to bring it to code with current criteria.”
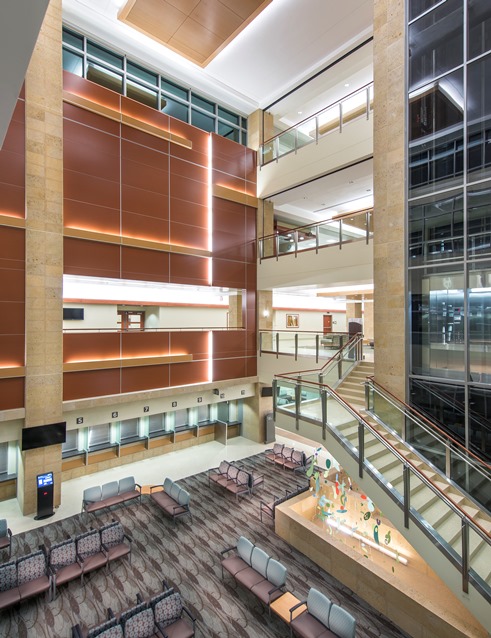
The design-builder, a joint venture of Clark Construction Group and McCarthy Building Companies, successfully met the owner’s requirements, as well as legally-imposed regulations. The hospital was to be a world class medical facility, larger in size, with more efficient operations, shifted from an in-patient to an outpatient operation, fitting into the adjacent residential neighborhood in appearance, and compliant with the UFC and anti-terrorism requirements. In addition, the Clark/McCarthy joint venture took responsibility for procuring and installing all the necessary medical equipment. And all of this was accomplished on a limited timeline.
“The previous hospital was not designed, and never retrofitted, to meet Anti-Terrorism/Force Protection (ATFP) requirements,” explained Carlos Gonzalez, Vice President with Clark Construction Group and Project Director of the Clark/McCarthy joint venture team. “The new hospital includes structural design, building envelope, security and Fire/Life/Safety measures to enhance protection for staff and patients in the hospital. The site master plan creates significant setbacks to prevent vehicles that may contain explosives from reaching the immediate adjacency of the building. The envelope components are designed to withstand a significant blast event, and in the event the envelope is compromised the damage is limited and the breakdown contained.”
By working as an integrated team – receiving outstanding evaluations for teamwork – and using design-build to its fullest, the project was delivered six months early and more than $100 million under the initial programmed amount.
“By having the design and construction team working together, from the onset of the project (and even prior to award during the proposal preparation phase), and with common goals and objectives, the team could quickly and efficiently evaluate options, discuss openly available solutions and arrive together at the best answer in an accelerated timeline,” Gonzalez continued. “The design-build setup also drove the idea that the team would be best served by co-locating and working together on a daily basis. This co-location included not only the design-build team, but also owner, end-users, jurisdictional authorities and community representatives. This co-location further enhanced the integration of ATFP requirements because when new information was discovered that required us to adapt our solutions, the co-located team was able to bring all stakeholders to the same physical table in a matter of minutes and stay in the room until a solution was developed that complied with all requirements and was feasible to construct.”
Using phased order and delivery, construction was faster than ever in NAVFAC’s experience. By receiving medical equipment just prior to installation, it went directly from the manufacturer into the hospital without being stored in a less secure warehouse. The new hospital was designed for efficiency and safety on both medical and physical fronts. A portion of the complex faces the Pacific Ocean and, with the innate protections, will be able to take advantage of the naturally beautiful view. Light and air are delivered by internal courtyards, protected by the building itself from external attack. The resident officer in charge of construction, called the design-build team, “a high performing team which continually planned for future project requirements and resolved every challenge from the trivial to the mind boggling.”
FY11 228PN Unaccompanied Enlisted Personnel Housing at Schofield Barracks
The Unaccompanied Enlisted Personnel Housing (UEPH) building at Fort Shafter in Hawaii presented some issues unique to its location. Being in Hawaii required that all materials for the facility be ordered well in advance to accomodate the long delivery time required. Fast-tracking and moving ahead before the design was complete allowed the design-builder, Absher Construction Company, to have the necessary materials on site when needed.
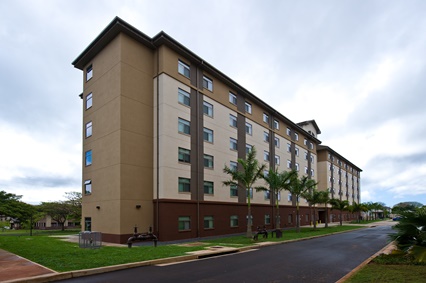
Because of a restricted available site area, the buildings required controlled access and built-in hardening. The design incorporated specific structural engineering for blast resistance and progressive collapse. These components and their installation reduced the chances of death or injury to occupants. The building uses reinforced concrete to strengthen the basic structure and connected to the structure are non-bearing partitions to resist displacement in the event of an explosion. All the non-structural components that could be dangerous in the event of a collapse – such as suspended ceilings, lighting, ducts, piping, conduits or large furnishings – have also been secured to the structure itself to prevent flying debris. Exterior windows are blast resistant and the design limits the danger of the glass separating from the frame, virtually eliminating the danger of injury from broken glass. The exterior doors consist of heavy, insulated metal with frames and hardware resistant to deflection. Even the sprinkler piping has been routed so that damage to the exterior walls will not affect it and internal fires can still be controlled.
Absher was able to introduce a number of innovations, one being the use of Insulating Concrete Forms (ICF) and ICF door frames. This method leaves the concrete forms in place, providing an additional layer of structural strength and insulation while reducing construction waste and shortening time spent on construction.
The end result is that the new housing facility meets – and perhaps goes beyond – the requirements for anti-terrorism protections. The design-build team was also commended for the high level of efficiency and cooperation. And the final facility should prove to be popular among the residents for its quality and comfort.
Battlespace Environmental Laboratory
The mission of the Battlespace Environment Division is to specify, forecast, mitigate and exploit the impacts of the operating environment on Department of Defense systems and operations focusing on space and atmospheric environments. As such, it has numerous highly technical elements that had to be included, many of which moved from a previous location. While the laboratory is located inside Kirtland Air Force Base, providing a substantial amount of security to start, the delicate scientific equipment and its importance to national defense required careful positioning to ensure that it was placed properly and securely. Throughout the project, the design-build team led by Burns & McDonnell Engineering Co., Inc., worked closely with the Corps of Engineers representatives to not only protect the equipment, but keep the project on schedule and within budget, even with a number of increases in scope.
Burns & McDonnell assembled a team of qualified professionals – including DBIA certified individuals, professional engineers and experienced construction professionals – to design and construct the two-story Battlespace Environment Laboratory (BEL), which supports more than 300 scientists and engineers. The $53.5 million project allowed the Battlespace Environment Division of Air Force Research Laboratory’s (AFRL) Space Vehicles Directorate to relocate the facility from Hanscom Air Force Base in Massachusetts and consolidate the majority of AFRL Space Vehicles activity to Kirtland Air Force Base in New Mexico. The unique nature of the work performed in the Battlespace Lab required the design to address all aspects of anti-terrorist/force protection as well as several specific facility security requirements.
“We assembled an integrated design-build team to create this secure, high-tech engineering laboratory,” says Mark Zimmerman, Design Manager at Burns & McDonnell. “This facility was required to comply with the Unified Facilities Criteria (UFC) 4-010-01 DoD Minimum Antiterrorism Standards for Buildings, as well as the DCID 6/9 Physical Security Standards for Sensitive Compartmented Information Facilities (SCIF). Our one team approach provided integrated project delivery, as well as efficient and effective communications with the Air Force’s security personnel. A diligent design team, a very cooperative and engaged client, and an exemplary field construction team attributed to smooth execution of the secured aspects of this project. From start to finish, the entire team had one vision in mind: make our client successful.”
During the design phase, the entire BEL team held weekly teleconferences with the client to keep topics current and make decisions in a timely fashion. In addition to the weekly design teleconferences, the BIM team met weekly to complete “clash and coordination” meetings. When construction started, the construction team conducted a bi-weekly teleconference with the design team. In addition, the field staff met on-site with the client weekly.