Issue 1 of 2016
Since the founding of the Design-Build Institute of America (DBIA), design-build has gone from a new, alternative project delivery method, to a standard option owners regularly turn to for best value in project delivery. So while DBIA will continue to promote the use of design-build where it is limited or unauthorized, more experienced owners are perfecting the design-build method itself. Over the past several years, the water/wastewater sector has been doing just that by steadily adopting Progressive Design-Build, and now the transportation sector is starting to do the same.
Have you heard? IQ now comes digital!
View this article in the digital version of our magazine by clicking here!
What is Progressive Design-Build?
As owners constantly reassess their design-build procurement, contracting and execution, questions arise such as how much of the design should they control and what is the risk of taking on responsibility for that design?
Progressive Design-Build (PDB) facilitates involvement of the design-build team during the earliest stages of the owner’s project development, ensuring they are part of the project team developing design solutions. This promotes the greatest amount of collaboration between the three key players in a construction contract – the owner, the designer and the contractor.
While a project design is usually 35 percent complete (or more) by the time a design-builder is procured in the traditional two-step design-build process, PDB adds the design-builder to the owner’s team even earlier in the design phase. When the design is somewhere between 50 and 75 percent complete, the design-builder issues a Guaranteed Maximum Price (GMP).
The other major feature of PDB is that the design-builder is selected almost entirely on qualifications. The later price gives some owners heartburn, but if anything there is more cost certainty for the owner. According to Lisa B. Choplin, the former chief of Maryland State Highway Administration’s Innovative Contracting Division and current Deputy Executive Director of DBIA, “Since the design-build team is working collaboratively with the owner in PDB, risks can be identified and mitigated earlier in the design phase resulting in a GMP that reflects the actual cost to construct the project.”
PDB in Water/Wastewater
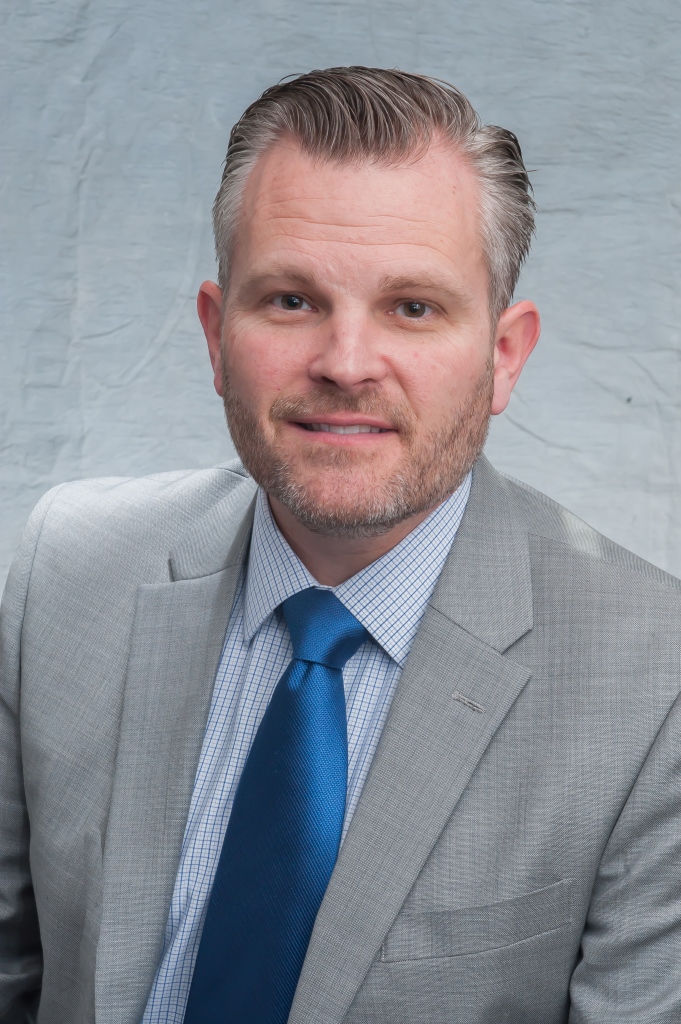
According to Bryan Bedell, Water Division Leader for Haskell, PDB has taken off at an accelerated pace in the water and wastewater market primarily due to the high level of collaboration the delivery method provides. “No other delivery methodology drives interaction between the owner and the design-builder as much as PDB,” Bedell said. “Owners find PDB allows them the highest level of input and control while allowing the design-builder the best possible environment to foster innovation.”
PDB allows for construction to start long before design has been finalized so the client can have uninterrupted production at their facility. According to Bedell, “the water/wastewater market is unique due to both the comparative complexity of our projects and the lack of repetitive duplication found in both transportation and vertical projects, which I believe accounts for its high rate of adoption.”
For example, the large Jacksonville, Florida, utility known as JEA recently used PDB for two components of their Total Water Management Program (TWMP): an upgrade to the Main Street Water Treatment Plant and Segment 2 of the conveyance system. Design-build teams evaluated and optimized potential solutions for the projects, which led to both projects’ scopes being heavily modified. “Ultimately JEA was able to evaluate and select a treatment solution for the WTP upgrade based not only on current capital costs but long range operation & maintenance costs and operational benefits,” said Bedell, who worked on the project for Haskell. “The client also touted early knowledge of project costs as a real advantage. PDB was able to reduce the complexity of The Segment 2 project, which saved millions of dollars and redacted the duration of the project.”
Now that the delivery method has successfully gained a large foothold in the water/wastewater sector, the transportation world is looking at it closely, and the first PDB highway project is about to begin in Maryland.
PDB in Transportation
While PDB has been used for transit and airport projects, there hasn’t been a PDB highway project yet.
“It took time for design-build to take its place in the highway industry,” says Choplin. “Now that DOTs are comfortable and more experienced with design-build, it is only natural for them to gravitate towards PDB, where they get all the benefits of design-build but at an earlier stage in the process.”
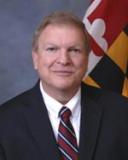
Under the leadership of Maryland Secretary of Transportation Pete Rahn, Maryland’s I-270 corridor project will be the first PDB highway project in the nation.
“Known as the Technology Corridor, I-270 is one of the most heavily traveled highways in the nation and is vital to Maryland’s economy and security,” said Secretary Rahn. “Traffic congestion solutions require the innovative minds of both our Maryland DOT public sector team and our private sector partners to work collectively on a range of options to provide the greatest benefit for travelers. We did not want to limit ourselves or innovative solutions in any way.” The State Highways Administration (SHA) therefore decided to rely on the engineering and construction industry to come up with innovative solutions to increase vehicle throughput, reduce delays and increase reliability along I-270. PDB was the perfect delivery method for this goal.
“The Maryland Department of Transportation (MDOT) recognized this is a bold project and would require a bold approach to successfully deliver it,”
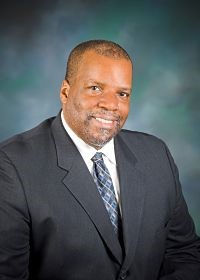
says Gregory C. Johnson, Administrator of MDOT’s SHA. “We did not believe a traditional design-build approach would provide the best solutions to reduce congestion on one of Maryland’s most heavily traveled corridors serving the nation’s capital region. We wanted a project where the best ideas from the engineering and contractor fields were all on the table and we could choose the best solutions to reduce congestion in this 30+ mile corridor. PDB was the only delivery method that will provide the desired outcome, including cost efficiency to MDOT, while reducing risk to potential design-build teams.”
Despite PDB being new to highways, Johnson said convincing others within MDOT to use it was not difficult. “The benefits of PDB to meet MDOT’s vision were obvious. We only had to ensure there were no procurement restrictions that would prevent PDB use. Fortunately, there are no statutory or regulatory related challenges.”
The two-phase, fixed-price contract will include design, right-of-way acquisition, utility relocations, construction services, and construction management services. There will be multiple standalone construction projects and therefore multiple GMPs.
By state statute, Maryland is required to include a price element in the selection process, so the state is taking into account “the reasonableness of price elements” in order to satisfy that requirement while still gaining the benefits of PDB.
“As part of the Price Proposal, each design-build team will provide its design and preconstruction fee and construction management fee with the balance of the fixed price being for physical construction for the project,” Johnson explained. “We will evaluate the price proposal to make sure the prices provided for each fee are reasonable for the scope of work proposed and that design-build teams are not unbalancing or front loading the items. Ultimately in selection, the Technical Proposals will be rated separately. Once consensus on technical ratings is reached, the price evaluation will then be considered through an integrated trade-off analysis. Considering the facts and circumstances of each Technical Proposal and the price, we will make a best-value selection.”
Johnson says SHA believes this selection approach, coupled with the openness of the contract scope, encourages the best technical and most innovative and creative solutions from each design-build team. “The selection is substantially weighted toward the Technical Proposals and, with the overall prices being fixed, the price would only affect selection if it is determined to be unreasonable.”
Will Its Popularity Continue?
The most commonly-voiced concern with PDB is that price is not a major factor for the selection of the design-build team. But Haskell’s Bryan Bedell says, “While it is true that the fixed price for the entire project is not a factor for selection in a PDB project, other pricing factors such as design fees, the design-builder fee, general conditions for the project or other pricing elements can be used as evaluation tools. Due to the absolute transparency of the open-book process utilized in PDB, owners can have absolute assurance that they have received the best market-driven pricing.”
Maryland’s Gregory Johnson thinks more owners should consider PDB, especially those who started using CM/GC. “Many owners, MDOT included, started using CM/GC for complex construction projects to provide scope flexibility, better mitigate and assign risks, shorten the project schedule and reduce costs,” he says. “The same benefits as CM/GC can be achieved from PDB, but with added benefits of design-build such as a single, contractual entity performing the design and construction. This provides better integration and communication for the project team than a CM/GC project. PDB also provides a better understanding and validation of the project scope for the design-builder before entering into a final price to construct. These benefits should ultimately provide a more cost-efficient project in a shorter time to owners.”